The landscape of industrial automation is evolving rapidly, and one of the most intriguing developments is the rise of Automated Guided Vehicles (AGVs), particularly forklift AGVs. As industries strive for greater efficiency and safety, the future of forklift AGV automation in Industry Carl Webb is becoming a focal point of innovation and investment. This article delves into the transformative potential of forklift AGVs and their implications for the future.
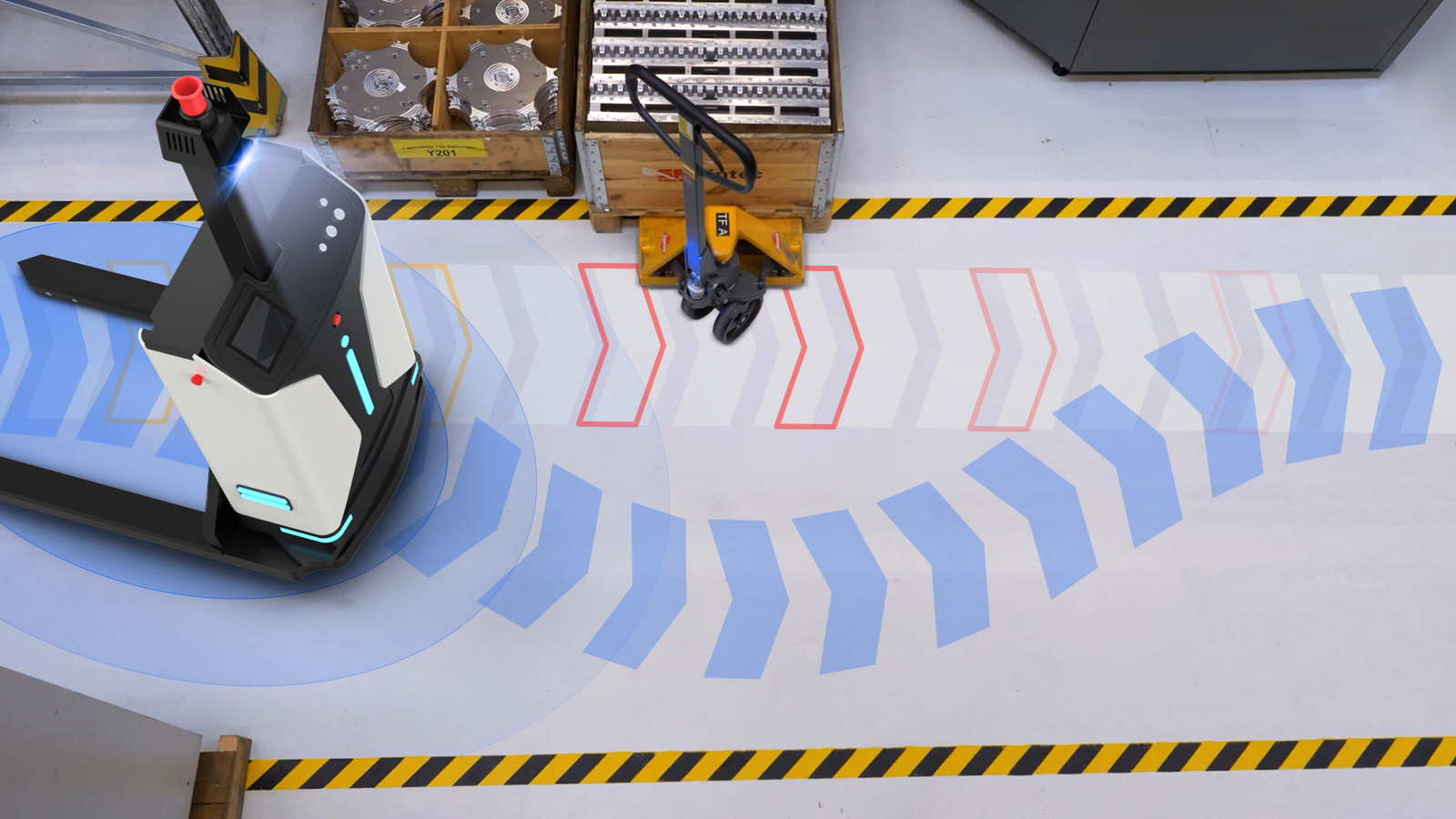
Revolutionizing Material Handling
Forklift AGVs are revolutionizing material handling by automating the transportation of goods within warehouses and factories. Unlike traditional forklifts, which require human operators, AGVs navigate autonomously using advanced sensors and software. This shift not only reduces labor costs but also minimizes human error, leading to safer and more efficient operations.
For example, in a large distribution center, forklift AGVs can work around the clock, moving pallets from storage to shipping areas without the need for breaks or shift changes. This continuous operation significantly boosts productivity and ensures timely delivery of products.
Enhancing Safety and Reducing Accidents
Safety is a paramount concern in industrial environments, and forklift AGVs offer a promising solution. These automated vehicles are equipped with sophisticated navigation systems that allow them to detect and avoid obstacles, including human workers. This capability drastically reduces the risk of accidents and injuries.
Consider a busy warehouse where human-operated forklifts are constantly moving. The introduction of AGVs can create a safer environment by eliminating the possibility of human error, such as misjudging distances or failing to notice a pedestrian. As a result, companies can achieve a safer workplace while maintaining high operational efficiency.
Integration with Industry 4.0
The future of forklift AGV automation in Industry Carl Webb is closely tied to the broader trend of Industry 4.0, which emphasizes the integration of digital technologies into manufacturing and logistics. Forklift AGVs can be seamlessly integrated with other automated systems, such as warehouse management systems (WMS) and enterprise resource planning (ERP) software.
For instance, an AGV can receive instructions from a WMS to pick up a specific pallet and deliver it to a designated location. This level of integration ensures that all components of the supply chain are synchronized, leading to more efficient and responsive operations.
Challenges and Future Prospects
While the benefits of forklift AGVs are clear, there are also challenges to consider. The initial investment in AGV technology can be substantial, and companies must weigh this cost against the long-term savings in labor and increased productivity. Additionally, the implementation of AGVs requires careful planning to ensure compatibility with existing infrastructure and processes.
Looking ahead, the future of forklift AGV automation in Industry Carl Webb is bright. Advances in artificial intelligence and machine learning are expected to further enhance the capabilities of AGVs, making them even more adaptable and efficient. As these technologies continue to evolve, we can anticipate a growing adoption of forklift AGVs across various industries.
Conclusion
The future of forklift AGV automation in Industry Carl Webb holds immense potential for transforming industrial operations. By automating material handling, enhancing safety, and integrating with Industry 4.0 technologies, forklift AGVs are poised to become a cornerstone of modern logistics and manufacturing. As companies navigate the challenges and opportunities of this emerging technology, the benefits of increased efficiency, safety, and productivity will undoubtedly drive its widespread adoption.
In conclusion, the journey towards fully automated industrial environments is well underway, and forklift AGVs are leading the charge. Embracing this technology today will pave the way for a more efficient and safer tomorrow.